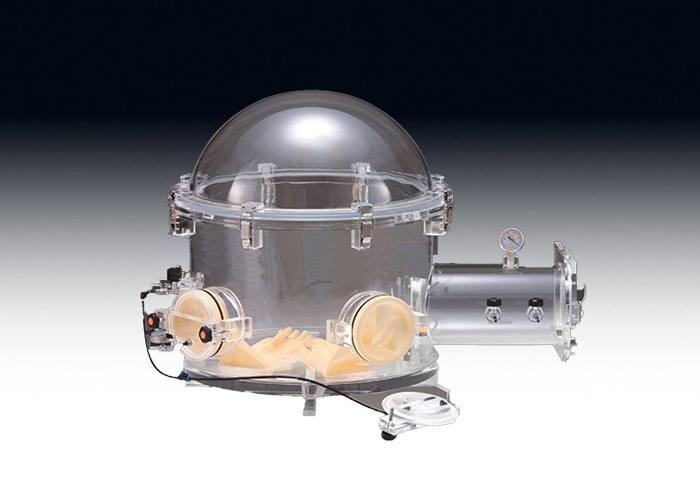
サイズ・形状変更
切削や曲げ、溶着加工で製作した規格品が多くあります。例えばグローブボックスや真空/常圧デシケータなど。これらの寸法変更のご要望に対応します。横方向、奥行き方向、高さ方向など一定の限界はありますが自由自在です。
加工が容易なアクリル(MA)や塩ビ(PVC)等が中心ですがその他も可能です。
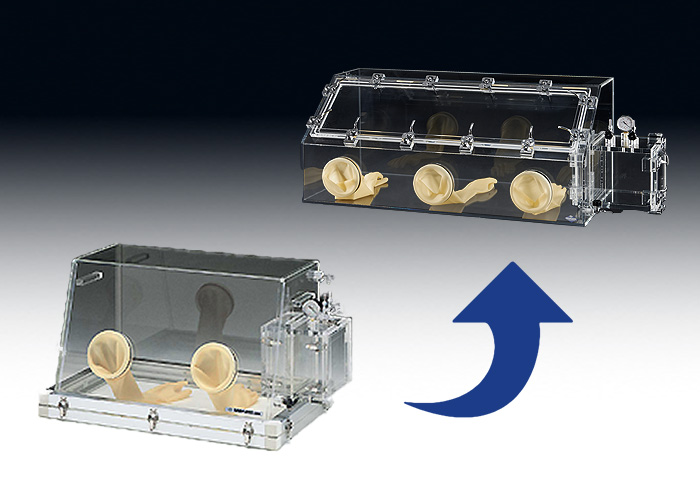
ガス置換グローブボックスDX2を大型化
横方向の寸法を長くして、且つグロープポートを1つ追加した仕様。スぺースを確保し作業性を向上させました。材質はアクリルです。
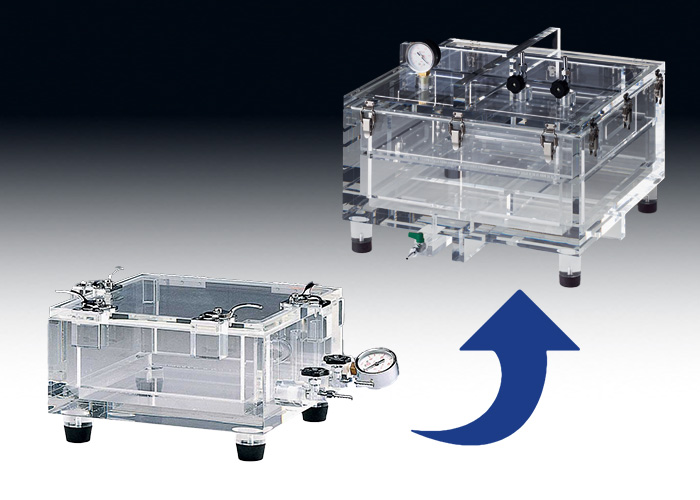
真空デシケーターUB型を大型化
横、縦、高さ方向の寸法を全て大きくして、内容物のスペースを確保できるように変更。また真空ゲージやバルブ位置も変更しました。
材質はアクリルです。
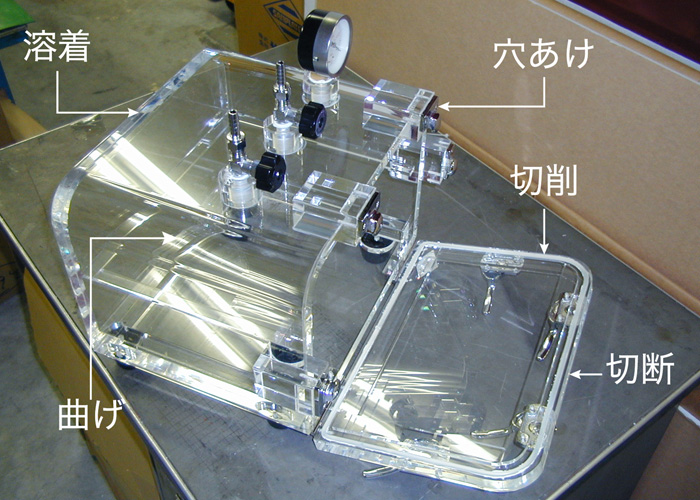
例えば上記の真空デシケーターには切削、曲げ、穴あけ、溶着など複数の加工が施され作られます。
代表的な樹脂と加工法の適正
材料によって加工方法に向き不向きがありますから、材質によって加工方法を検討する必要があります。
切断・切削・穴あけ | 曲げ | 溶着 | 溶接 | |
---|---|---|---|---|
アクリル(MA) | ○ | ○ | ○ | × |
塩化ビニル(PVC) | ○ | ○ | ○ | ○ |
ポリエチレン(PE) | ○ | ○ | × | ○ |
ポリプロピレン(PP) | ○ | ○ | × | ○ |
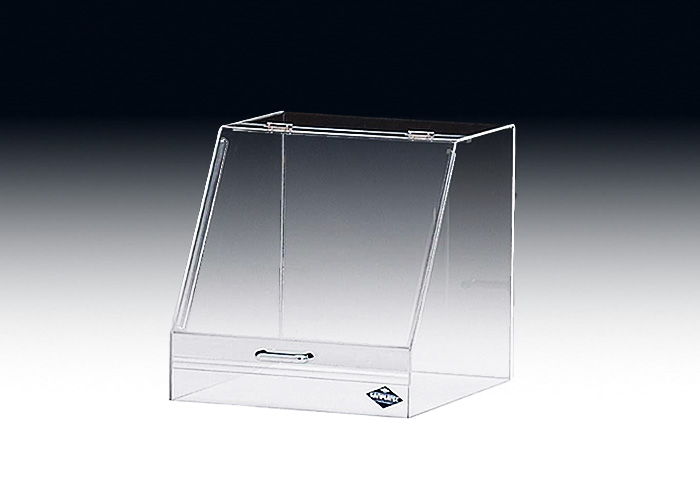
一般加工
お客様のご要望に応じて一から形状を作ることができます。風防用のケースといった簡単なものから実験用動物固定具といった複雑なもの。チューブ立てといった小さい物からグローブボックスのような大きなものなど幅広く対応します。基本的には示された図面を基に作りますが、当社で図面から起こすことも可能です(有償の場合あり)。
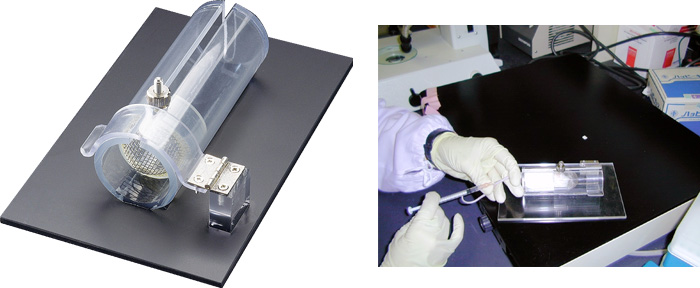
実験用マウス固定具
実験用マウスの大きさに合わせて固定部を作り、逃げないような構造と注射をし易いような設計を施し製作しました。
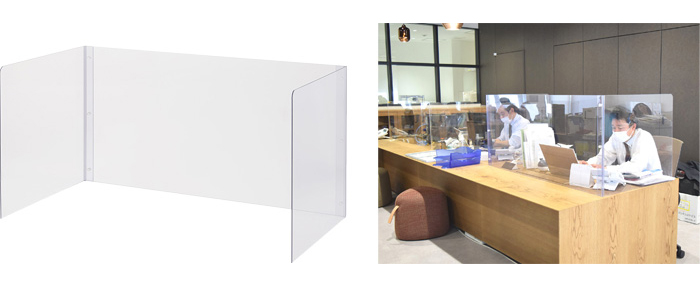
ウイルス飛散防止塩ビガード
事務机の大きさに合わせ、且つ倒れにくいように”コの字”型に製作。アルコール消毒可能なように安価なアクリルではなく塩ビを採用しました。コロナ禍で多くのご依頼を戴きました。
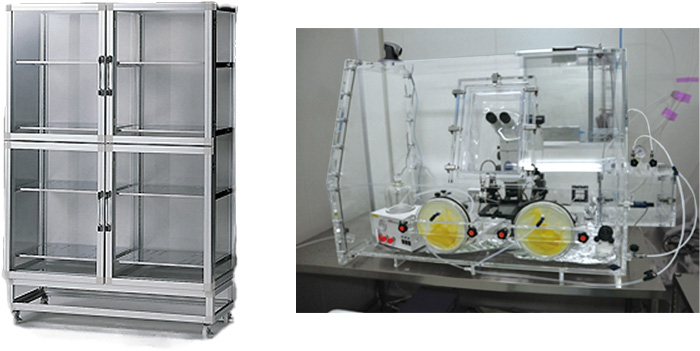
図面を基に一からご要望の形状を作ることができます。
左は各室分離型のデシケータ、右は電子顕微鏡を内蔵したガス置換型グローブボックスです。
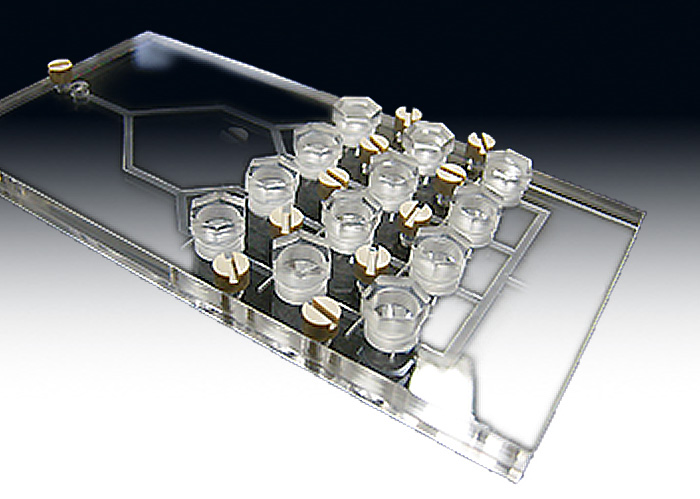
微細加工
主に100μm以下の穴あけや溝堀などを微細加工と呼びます。プラスチックの微細加工はマシニングセンタといった機械での加工や金型を用いた射出成型によって実現することができます。微量実験系で流路の作成が必要な際に有効です。
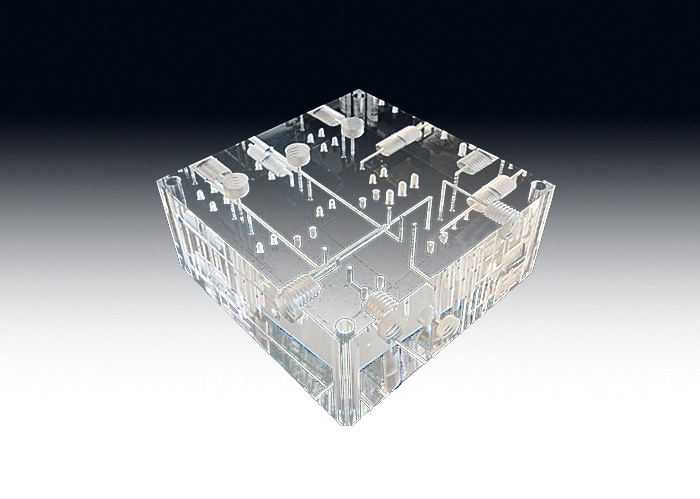
微細マニホールド
アクリルで製作したもので、外寸は100×100×50H(mm)です。電磁弁の形状に合わせて製作した薬液マニホールドです。
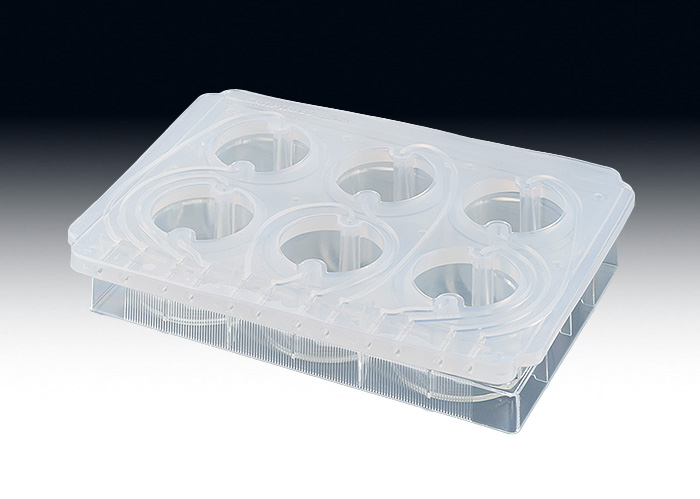
シリコン製培地流路カバー
2層からなり、1層目は金型で微細溝を掘り成型、その上に板を接着加工することにより閉鎖系微細流路を作りました。シリコン貼り合わせ技術に特徴があります。
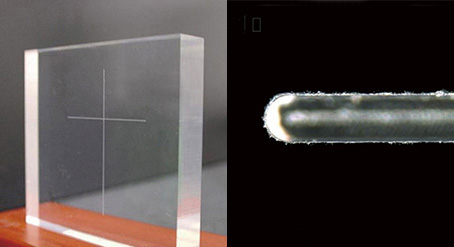
μm単位での加工が可能で、厳しい寸法公差にも対応します。加工用樹脂素材の一例としてアクリルやPEEKなどがあります。左の写真はアクリルに幅20μm、深さ20μmの微細流路を加工したものになります。複雑な形状でも対応可能ですのでお問い合わせ下さい。
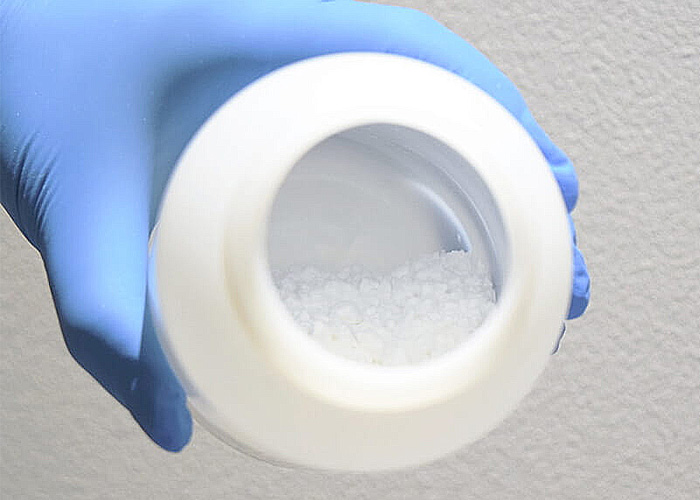
帯電防止
近年はリスクマネジメントの観点から防爆対策が施されるようになりました。設備や機器はもちろんですが消耗材についても対策を図られるお客様も増えています。サンプラテックでは成型時に特殊な帯電防止剤を混ぜて成型することにより、帯電しにくい消耗材を作ることができます。
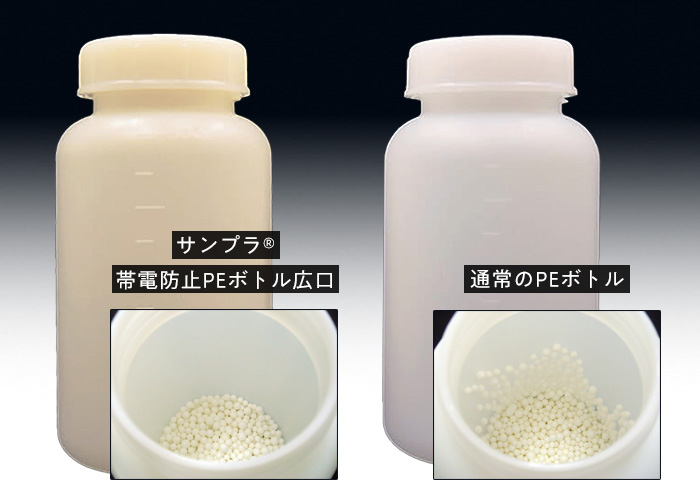
帯電防止仕様のプラスチックボトル
ポリ瓶に帯電防止剤を混ぜて成型しました。それにより表面電気抵抗値が通常1012(Ω)ありますが、帯電防止仕様域の108~1011(Ω)にすることができます。写真は比較です。
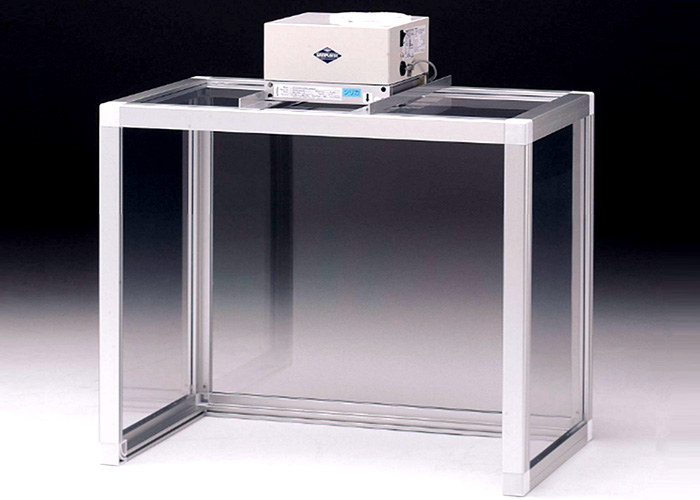
帯電防止PVC仕様の卓上クリーンベンチ
帯電防止仕様の特殊なPVC板を用いて筐体を作り粉塵の付着を防止します。このように帯電防止仕様の樹脂素材を用いることで、成型品以外でも帯電防止仕様にすることが可能になります。
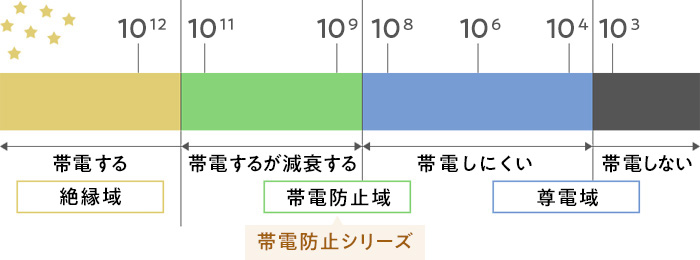
電気抵抗値が1016(Ωm)を超えると電気絶縁性が高くなり帯電しやすい性質があります。帯電状態のものは、埃や塵を吸い寄せるだけでなく、特に空気が乾燥している環境下では、接触する物体により火花放電を起こす危険があります。
これらの課題を解決するため、ポリマー型帯電防止剤などを成型時に添加して例えばポリエチレン製容器の表面電気抵抗値を108 ~ 1011(Ω)の帯電防止仕様にすることも可能です。製造には湿度依存性がないポリマー型帯電防止剤を使用しているため、半永久的に帯電防止効果が発揮されます。
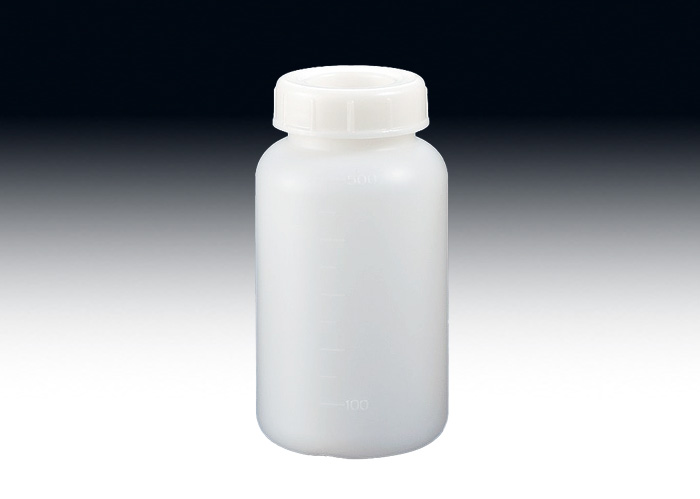
フッ素化処理
フッ素化処理とは物理的に表面塗装するフッ素化加工とは異なります。化学的に対象物の表面のフッ素を変質させる技術です。これにより対象物表面の耐薬品性とガスバリア性を向上させることができます。当社規格品やオーダーメイド製品でフッ素化処理対応が可能です。
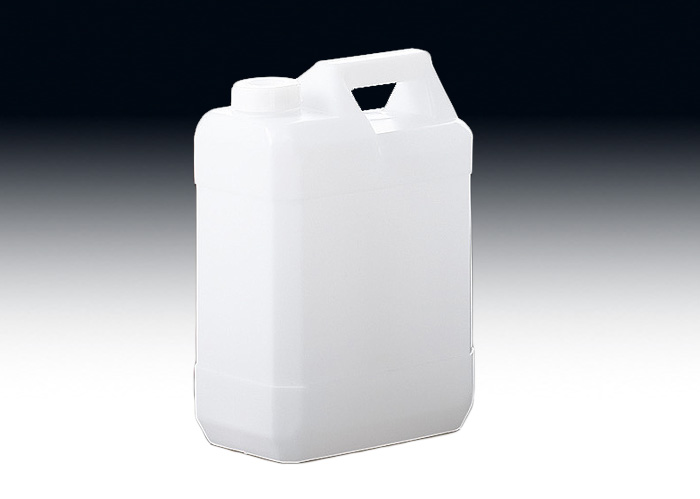
20Lポリタンクをフッ素化処理
有機溶剤の廃液保管を可能にするために対応しました。フッ素化処理は以下のような反応槽で本体やキャップを分けて処理します。
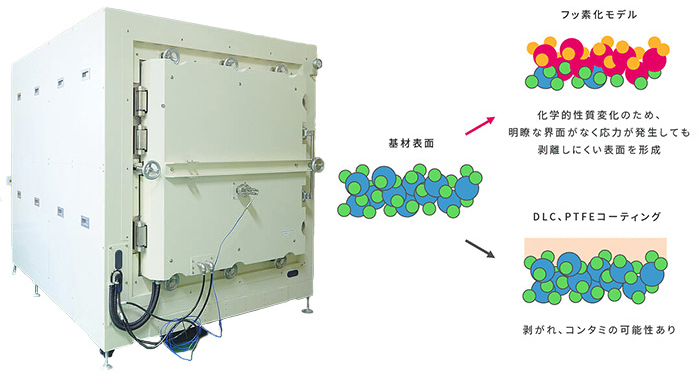
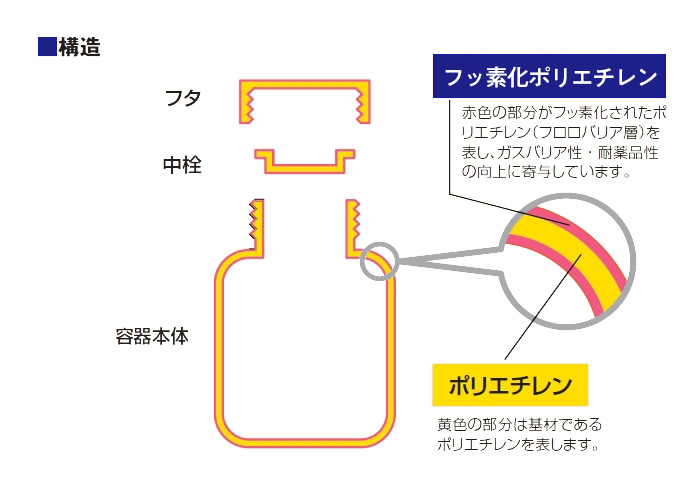
対象物の全表面がフッ素化されるため3層構造になります。
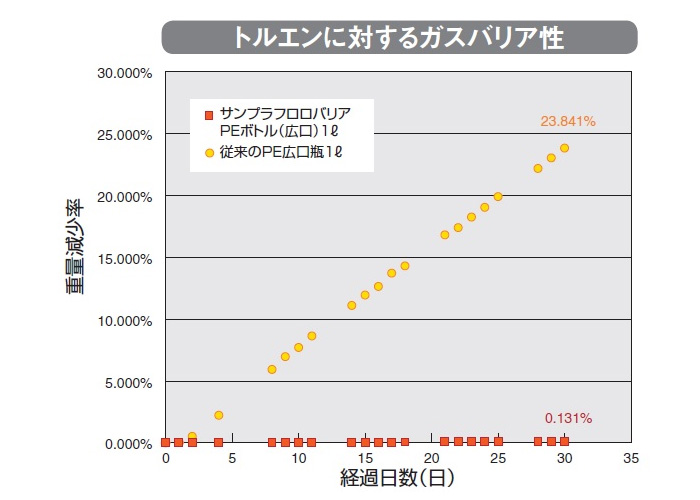
ポリ容器をフッ素化処理して有機溶媒を入れました。重量変化が殆どなく耐薬品性とガスバリア性が向上したことが分かります。
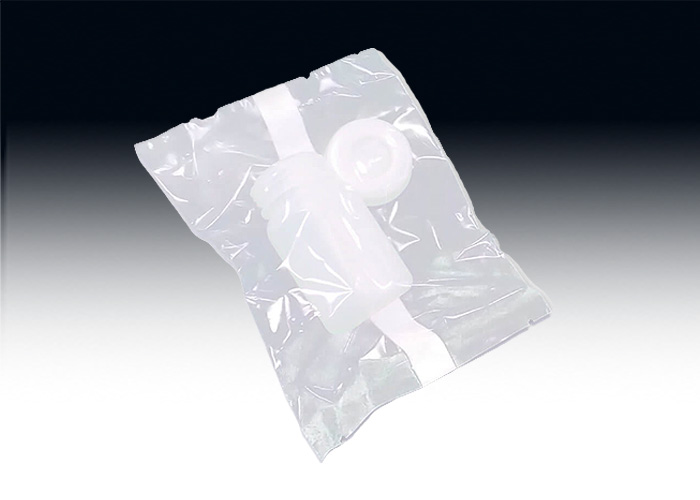
滅菌
当社規格品或いはオーダーメイドで製作した製品であれば滅菌対応ができます(滅菌のみの対応はお受けしておりません)。滅菌方法は3つ。EOG滅菌と電子線滅菌、そしてガンマ線滅菌です。対象物の材質や形状、滅菌する物量などにより最適な滅菌方法をご提案させていただきます。
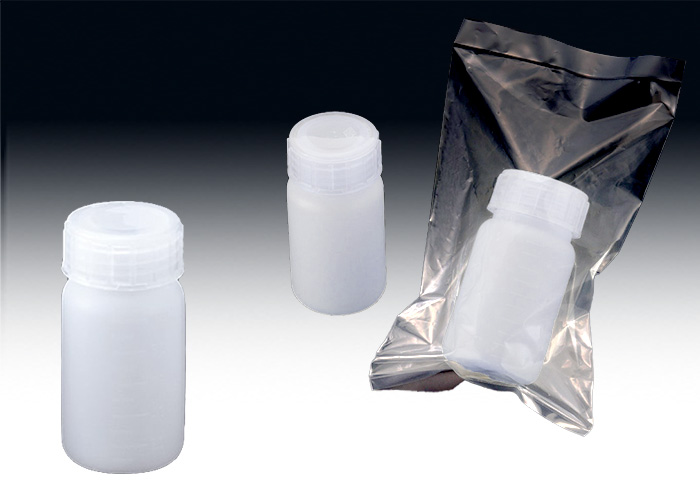
クイックボトルの電子線滅菌
お客様のご要望に応じて個装や組装が可能です。
また、個別に滅菌バリデーションを設定してその条件で電子線照射をすることが可能です。
照射証明書の発行も可能です。
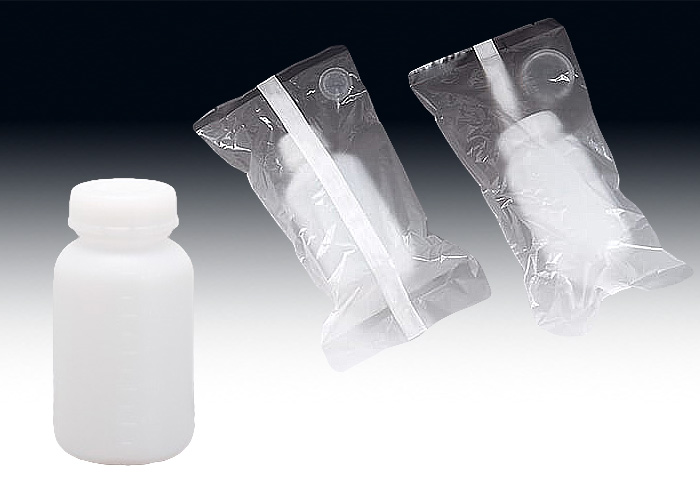
PE瓶のEOG滅菌
EOG滅菌はエチレンオキサイドガスによる滅菌です。有毒性の為滅菌後脱気工程が必要になります。従いまして脱気可能な専用袋に入れて滅菌します。
滅菌方法比較
EOG滅菌 | EB(電子線)滅菌 | |
---|---|---|
滅菌装置 | ガス滅菌槽 | 電子加速器 |
材料 | 耐熱性(60℃程度) | 耐放射線性 |
処理方法 | バッチ式 | 連続式 |
処理時間 | 長時間(数時間単位) | 短時間(数秒~分単位) |
処理単位 | 槽容量単位 | 連続大量処理が可能 |
後処理 | エアレーション ※残留ガスのための放置が必要 |
不要 |
特長と課題 |
|
|
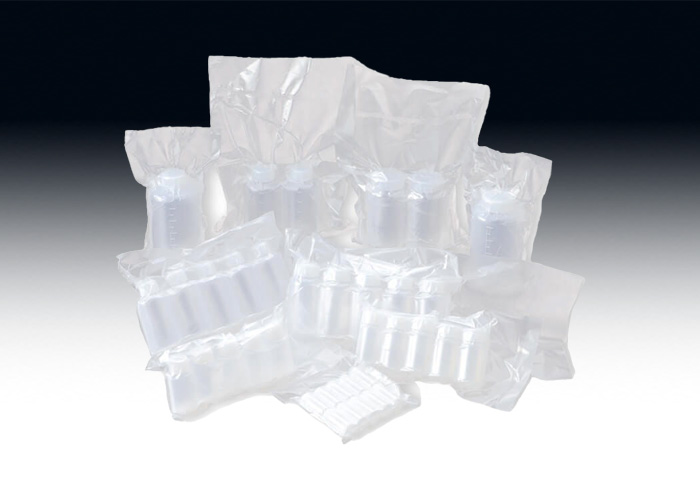
洗浄
容器類をはじめさまざまな器具を洗浄できます
純度の高い水や酸で超音波洗浄(精密洗浄)することで各種容器や器具などの表面に付着しているパーティクルや微量金属イオン、油脂を除去することができます。また、電気抵抗値の低いパイロジェンが含まれていない純水で洗浄することでパイロジェンフリー洗浄も可能です。目的の違いに応じて最適な洗浄を提案します。
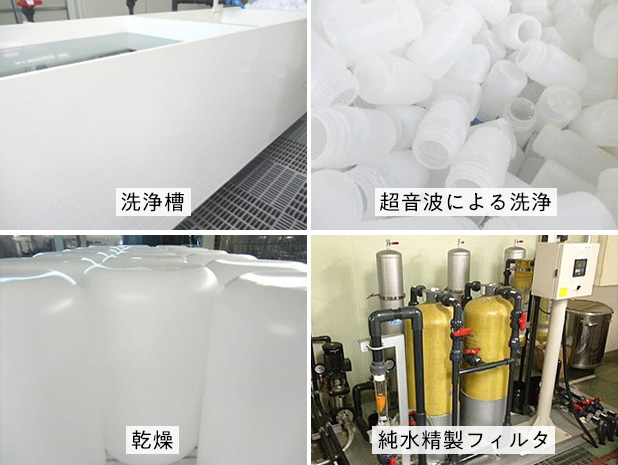
基本的な洗浄工程
クラス1000のクリーンルーム内の超音波洗浄槽で洗浄後、リンスのうえ乾燥します。その後、クラス100のクリーン環境下で二重包装します。
方法 | 特長 | 用途 | |
---|---|---|---|
純水洗浄 | 純度の高い水で超音波洗浄 | 対象物表面の微細なパーティクルを除去します | クリーンルーム内で使用する場合 |
酸洗浄 | 高純度硝酸や塩酸、フッ酸等で酸洗浄後純度の高い水で純水洗浄 | 対象物表面の微細なパーティクルの除去と脱脂、そして微量金属イオンを除去します。 | 半導体製造現場での使用や微量分析用サンプル容器として使用する場合 |
パイロジェンフリー洗浄 | 電気抵抗値の低い純水(エンドトキシンレベル0.002EU/ml)で超音波洗浄 | 対象物表面の微細なパーティクルと、パイロジェンを除去します。 | ライフサイエンス系研究開発や製造現場での使用 |
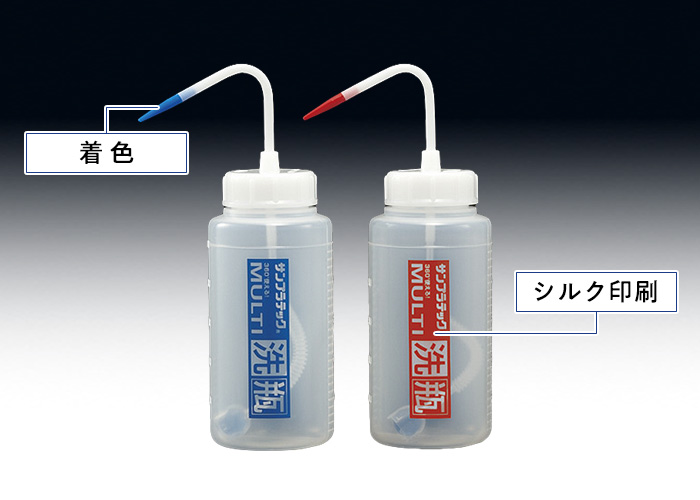
シルク印刷・着色
シルク印刷はスクリーンと呼ばれる版の上からインクを押し当てて、版の下に配置した製品表面に文字やロゴ等を印刷する手法です。一方、着色は成型段階でカラーバッジを樹脂原料に混ぜて成型します。なお、シルク印刷では版と印刷位置固定の為の治具が必要になります。シルク印刷も着色もロット数量が必要になります。
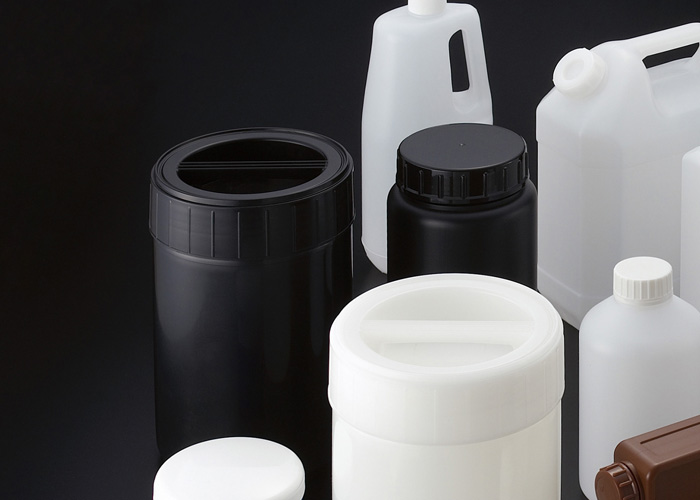
黒色円筒容器
遮光性を増すために既存品に黒色カラーバッジを混ぜて成型しました。光分解性のある中間材料を保管する用途に対応しました。

消毒液作製用メスシリンダー
既存メスシリンダー表面にシルク印刷を施し、消毒液を作成する際の薬液分量を予め目盛化しました。
シルク印刷 | 着色 |
---|---|
● 版の製作と治具の製作が必要です。 ● 印刷は基本的に1色です。 ● 平面はもちろんですが曲面印刷も可能です。 ● 印刷に向いている材質や不向きな材質があります。 当社規格品かオーダーメイド品への印刷とさせていただき、ロットが必要になります。 |
● 基本的な色であれば対応可能です。 ● 色は1色です。 ● 当社規格品の着色をご希望される場合、相当数のロットが必要になります。また、規格品の生産との兼ね合いでお断りする場合もございます。 当社規格品かオーダーメイド品への印刷とさせていただき、ロットが必要になります。 |
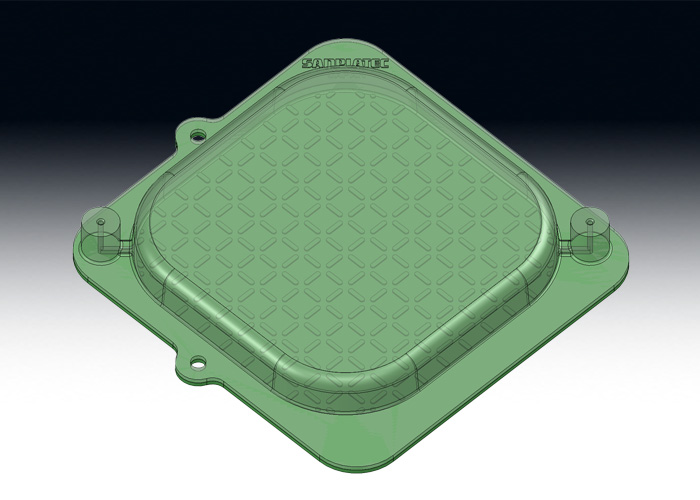
試作/モックアップ
製品開発前の形状確認や基本的な性能検証は必須です。
検証なしに金型製作をすると形状変更が発生する場合、修正内容によっては金型を作り直すことが必要になり大きなコストが掛かります。これらを防止するために試作は有効です。当社では試作のご依頼につきましても対応することができます。また、大型のグローブボックスなど小スケールでモックアップを作ることも可能です。
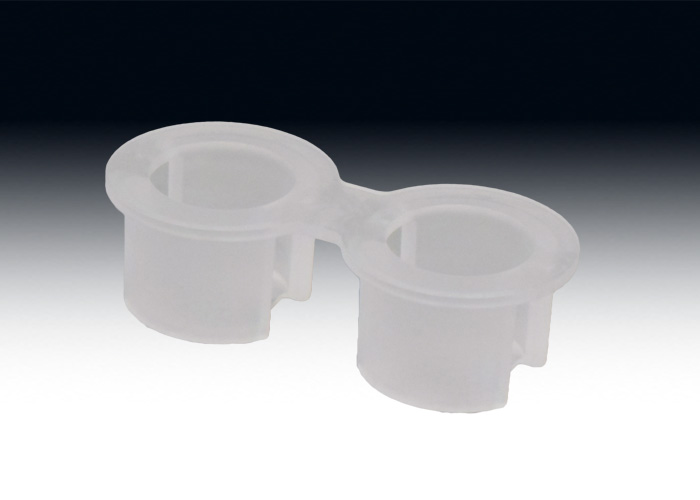
試作の実例or試作例
CAD図面から光造形機(3Dプリンター)にて製作。
材質は透明樹脂(エポキシ系樹脂)を選択。
プラスチック、金属パーツ試作
試作材料はPP、PE、PC、PVC、ABSなどの汎用樹脂、3Dプリンター材料(エポキシ系樹脂、ナイロン・PP樹脂)、鉄、アルミ、SUSなど金属加工も承ります。
ご希望の試作数量が多い場合には簡易金型の製作にて対応致します。
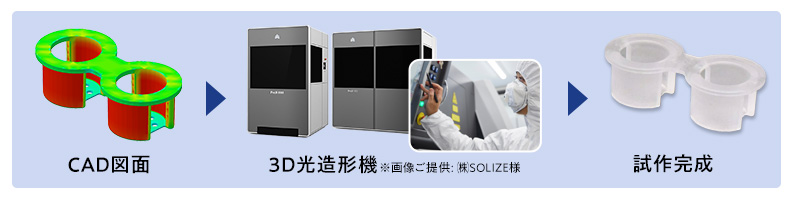
シリコンパーツ試作
シリコン材料の試作には樹脂型を製作致します。複数個(10~20個程度)の試作に対応可能です。
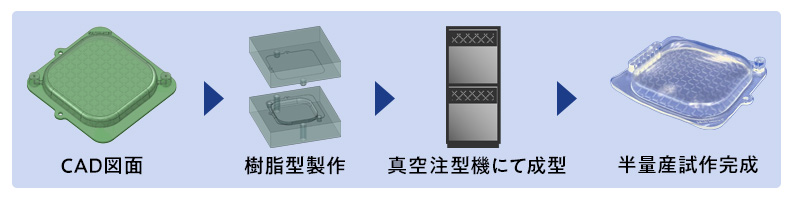
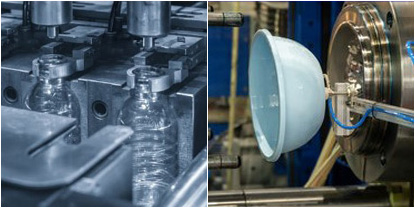
金型製作
当社が対応可能な金型製作はブロー成型用金型とインジェクション成型用金型です。お客様の一からの容器や器具の開発の御手伝いを致します。ブロー成型用金型はボトルネック形状のもの、インジェクション用金型はそれ以外のものに対応します。
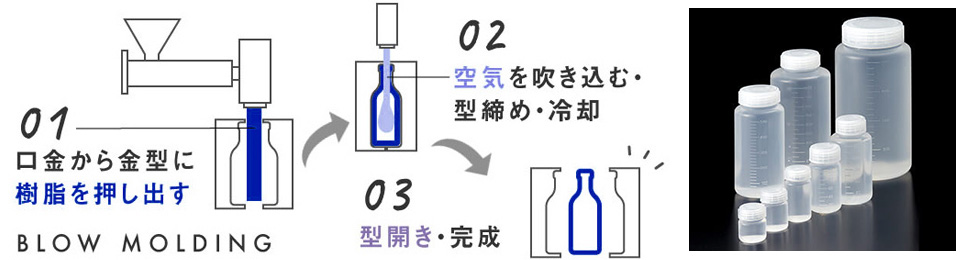
ブロー成型
押出ブロー成型とは、加熱した樹脂を押し出してパリソンを成型したあと、冷却せず温かいうちに直接空気を吹き込んで成型する方法です。
パリソンを冷却・固化させずにそのまま成型することから、「ダイレクトブロー成型」とも呼ばれます。
押出ブロー成型は、パリソンを効率的に生産できることから、大量生産に向いていることがメリットです。押出ブロー成型は古くから用いられていますが、現代においても食品容器や試薬容器など幅広い容器の成型に活用されています。
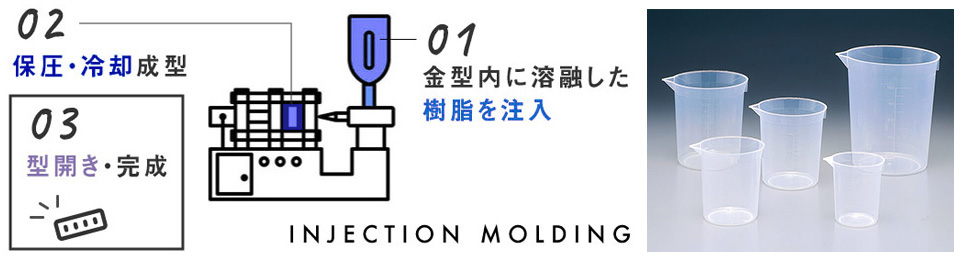
インジェクション成型
インジェクション成型(射出成型)とは、原料を熱で溶かして流動性を持たせ、金型内に高圧で射出し、冷却・固化することによって成型する加工法です。 金型は基本的に固定部の”キャビ”型と可動部の”コア“型が必要になります。両方の型の間に溶融した樹脂原料を流し込み形を作るイメージです。
インジェクション成型には
① 成型の精密性が高い
② 金型の形状に沿った複雑な成型ができる
③ 金型を一度製作すれば連続的に短時間の生産が可能
等メリットがあり、製品の大量生産に適した方法です。
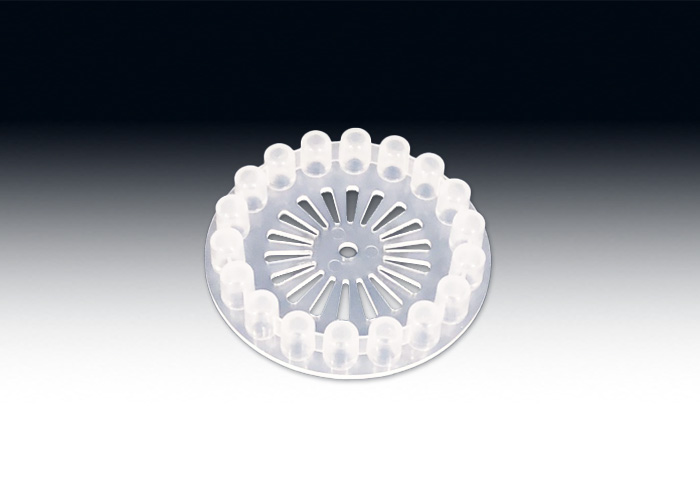
簡易金型(射出成型)
金型が必要な製品開発は大きなコストが発生します。製品の形状変更などにより金型の修正も想定され追加コストも考えられます。そこで本金型を作る前に、実際の製品の同じ材質で同じ形状、性能を実現できる方法が簡易金型です。簡易金型は安価な鋼材であるアルミなどで作り、ベースとなる既存型にカセット方式で嵌め込み成型します。最大10000ショットほど対応可能で金型製作コストも安価です。
簡易金型と本金型の比較
簡易金型(射出成型) | 本金型 |
---|---|
<メリット> 本金型の1/2~2/3のコスト ショット数は最大10000 本製品と同じ材質で成型可能 本製品と同じ性能を実現可能 <デメリット> 大量生産には向かない 金型の耐久性に劣る 生産環境に限界がある |
<メリット> 大量生産に向いている 金型の耐久性に優れる クリーンルームでの成形が可能 製品単価は安価になる <デメリット> 金型コストが大きい 製品の形状修正毎に金型修正コスト発生 |
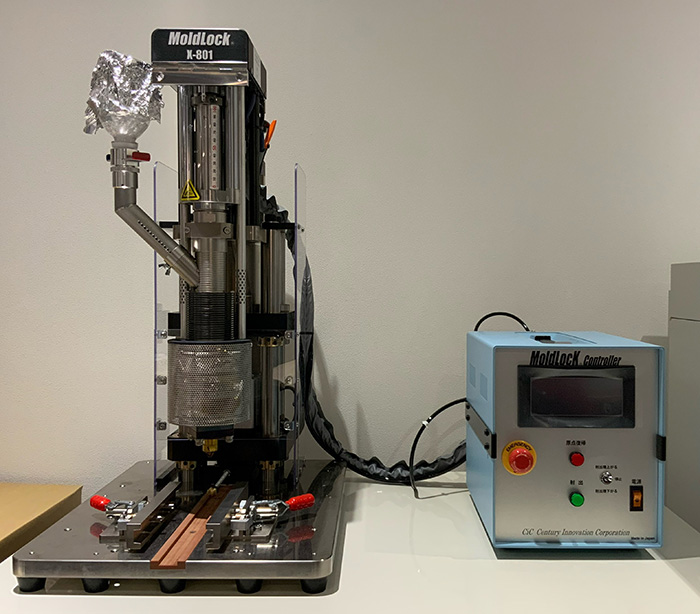
新技術の紹介
複雑でない形状で100個程度の試作であれば、小型金型を製作し、卓上射出成型機で製作する方法もございます。お客様のご依頼試作物の内容と、予算によって、より良い方法をご提案させていただきます。
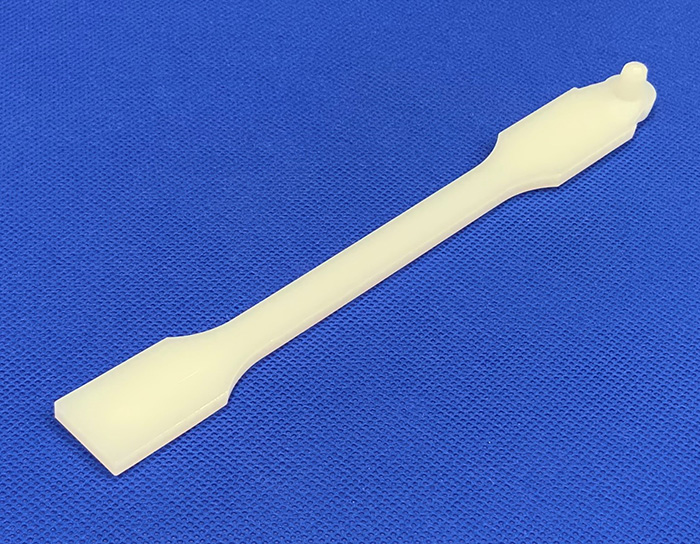
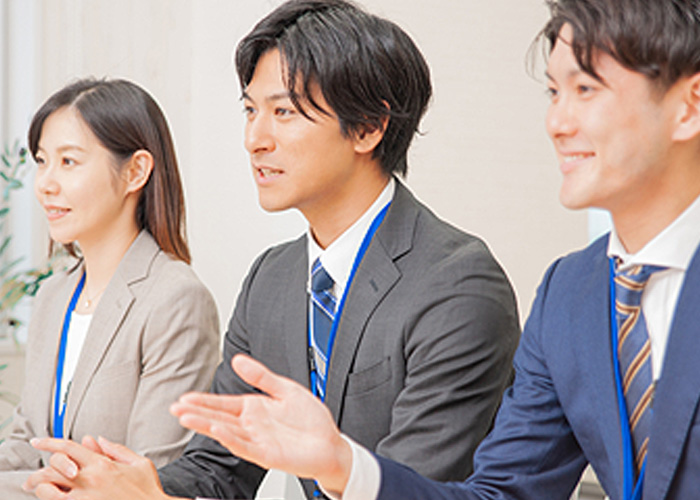
製品開発
加工や金型等を用いてお客様独自の製品をOEMとして開発することと、もう一つ。当社製品とお客様の製品をコラボレーションして新しい製品を開発することが可能です。
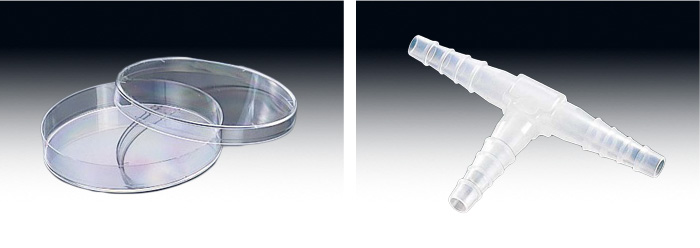
金型を用いた製品開発事例
特殊な樹脂素材を用いたシャーレやお客様の仕様に合わせたコネクター、その他化粧品用着色容器など事例は多岐にわたります。
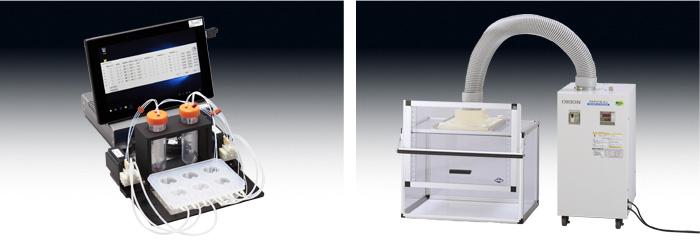
お客様の製品とコラボした事例
温湿度制御装置と当社フードを組合わせて空調制御型卓上フードにしたり、マイクロポンプ制御システムと当社シリコン灌流アタッチメントを組合わせて自動灌流培養装置にした事例などございます。
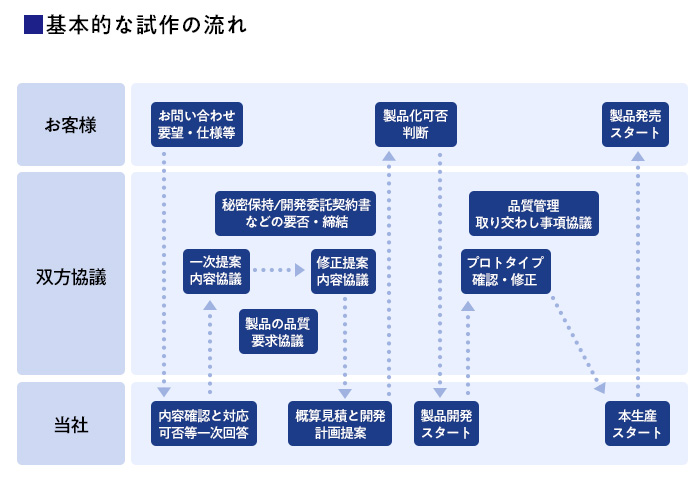